The automotive sector is poised for a transformative shift. Quantum computing, AI, and robotic manufacturing are revolutionizing vehicle design, construction, and energy efficiency. This evolution heralds a new era of automotive innovation and energy efficiency.
Electric vehicle sales are anticipated to skyrocket, with a projected sixfold increase from 2021 to 2030. This surge is driven by quantum technology advancements, which could generate up to $63 billion in value for the automotive industry by 2035.
Quantum computing holds the potential to revolutionize optimization and simulation in the automotive sector. It is poised to transform vehicle design, manufacturing processes, and operational efficiency. Quantum algorithms can simulate how material composition changes affect vehicle performance with unprecedented speed and precision.
As the industry advances, robotic manufacturing and AI-powered solutions are becoming crucial to production lines. These technologies enhance productivity, improve quality control, and elevate safety standards. The future of car manufacturing is quantum-powered, AI-driven, and robot-assisted.
The Rise of New Quality Productive Forces in Automotive Industry
China’s initiative to enhance new quality productive forces is revolutionizing the automotive industry. During his 2023 visit to Heilongjiang, President Xi Jinping underscored the importance of this shift towards strategic emerging sectors. The automotive industry, pivotal in this evolution, is experiencing unprecedented innovation-driven growth.
In 2023, China’s production of new-energy vehicles skyrocketed to 9.44 million units, representing a 30.3% increase from the previous year. This exponential growth underscores China’s dedication to technological advancement in the automotive realm. The emphasis on innovation is propelling significant strides in vehicle production and design.
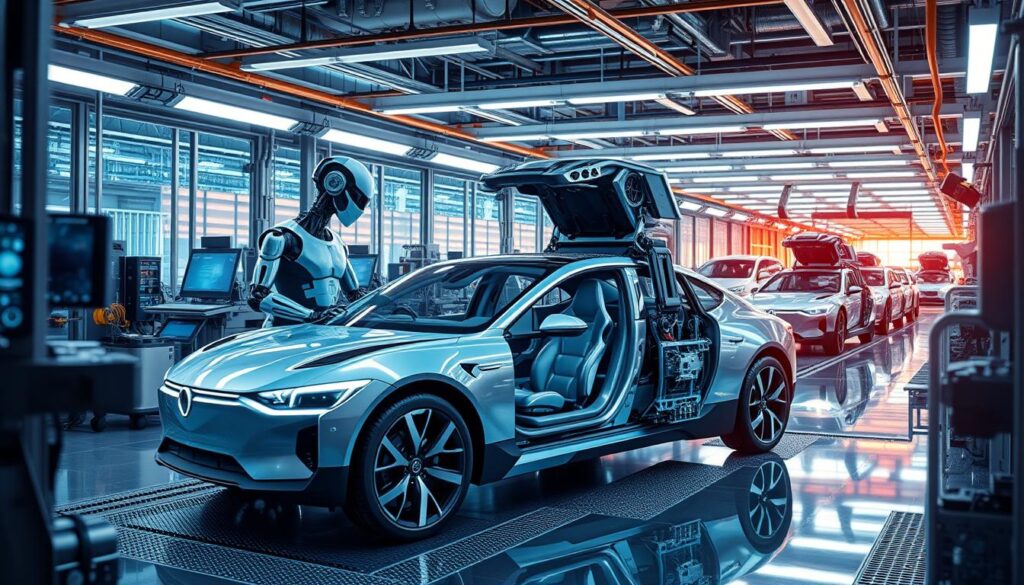
The government’s backing for strategic emerging sectors is clear through recent policy shifts. In January 2024, a coalition of seven ministries, spearheaded by the Ministry of Industry and Information Technology, unveiled a list of “future industries.” This initiative is in line with China’s vision for technological progress across sectors, including automotive manufacturing.
The automotive industry’s metamorphosis is integral to a larger national strategy. China’s Innovation-Driven Development Strategy seeks to position the nation as a global leader in science and technology innovation by 2050. This lofty objective is fueling substantial investments in research and development, thereby cultivating a culture of innovation within the automotive sector.
Quantum Computing: Revolutionizing Automotive R&D
Quantum computing is transforming the landscape of automotive research and development. This advanced technology facilitates swift and precise material simulation, thereby accelerating battery development and chemical interactions analysis. Automotive firms are collaborating with quantum computing entities to enhance these processes, aiming to reduce the lengthy and costly product development cycles.
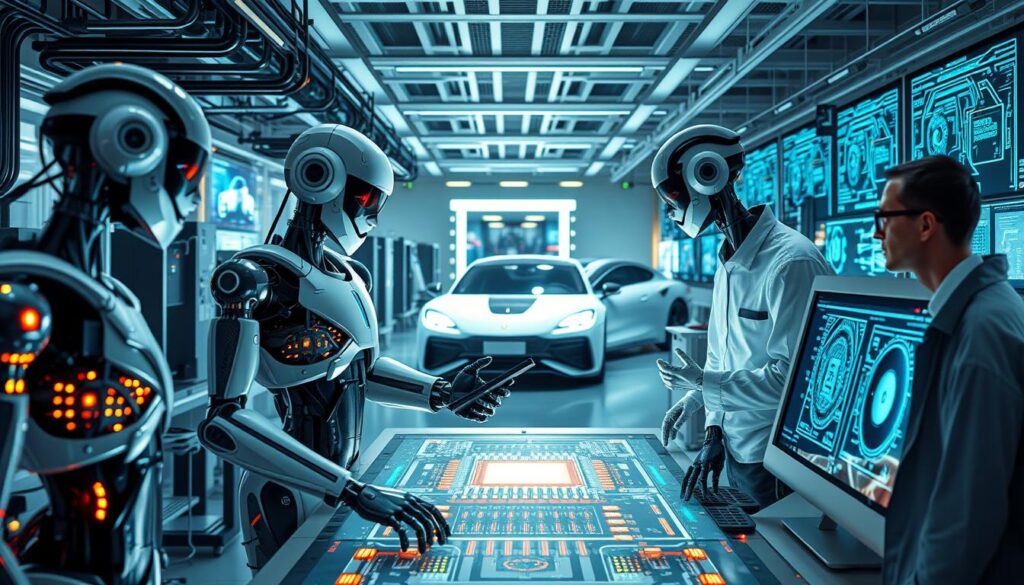
A recent study by Zapata Computing, BMW, and MIT’s Center for Quantum Engineering highlighted the efficacy of quantum-inspired methodologies in optimizing vehicle production. Their Generator-Enhanced Optimization (GEO) method surpassed conventional problem solvers in 71% of instances, underscoring its potential to revolutionize the sector.
The influence of quantum computing transcends mere production efficiency. It is propelling the advancement of self-driving vehicles and refining material discovery for electric vehicle batteries. Quantum computers excel in modeling intricate molecules, making them indispensable for chemical interactions research in automotive contexts.
With substantial investments from governments and private entities, quantum technology’s significance in automotive R&D is poised to escalate. Experts forecast that quantum computing could generate nearly $1.3 trillion in value by 2035, with a considerable share benefiting the automotive industry. This technology heralds a new epoch of innovation in material simulation, battery development, and chemical interactions analysis, setting the stage for a transformative era in the automotive sector.
AI-Powered Solutions Transforming Vehicle Production
Smart manufacturing is revolutionizing the automotive industry. At the core of this transformation are industrial AI and production optimization. McKinsey Global Institute suggests that 30 percent of activities in 60 percent of U.S. and German occupations could be automated. This shift is anticipated to boost Germany’s GDP by up to 4 percent by 2030.
In vehicle production, AI-based machines outperform humans in defect detection by 90 percent. This significant improvement in quality control is essential for automakers aiming to enhance agility. AI-powered forecasting in supply chains can reduce errors by 30 to 50 percent and inventory levels by 20 to 50 percent.
AI-driven production optimization is delivering substantial outcomes. QuantumBlack’s AI methodology enhances R&D productivity by 10 to 15 percent and accelerates time to market by 10 to 40 percent. These advancements are crucial as the industry transitions towards electric and software-defined vehicles, which increases costs.
The effects of smart manufacturing extend beyond the production line. The rise of online car-buying is compelling dealerships to invest in digital experiences. This comprehensive transformation, fueled by industrial AI, is establishing new benchmarks in automotive manufacturing efficiency and innovation.
Car Manufacturing With Quantum Computing. Humanoid Robots, AI and Energy Saving
The automotive sector is entering a new phase of energy-efficient manufacturing. Quantum computing, humanoid robots, and AI-driven production are transforming car assembly lines. These innovations aim to enhance efficiency and diminish energy usage in vehicle production.
Robotic assembly is becoming prominent in car factories. Entities such as Figure and 1X are pioneering advanced humanoid robots for automotive manufacturing. Already, BMW and Mercedes-Benz are piloting these technologies on their assembly lines. Tesla is concurrently developing its humanoid robots to refine its manufacturing processes.
AI-driven production systems are redefining the automotive industry. These intelligent systems refine production schedules, scrutinize quality control, and manage inventory with unparalleled precision. By harnessing AI, car manufacturers can drastically cut down on waste and elevate overall productivity.
Energy-efficient manufacturing is paramount for automakers. Quantum computing is pivotal in this endeavor by optimizing intricate production processes. It facilitates the design of more aerodynamic vehicles, enhances battery efficiency for electric cars, and streamlines supply chain logistics. This amalgamation of avant-garde technologies is setting the stage for a more sustainable and efficient automotive industry.
Generative Design: Speeding Up Automotive Innovation
Generative design tools, empowered by AI, are significantly altering the automotive landscape. These sophisticated systems enable engineers to set design objectives and parameters, subsequently exploring an immense array of possibilities to propose optimal designs. This AI-driven methodology is fundamentally changing how products are validated and optimized within the industry.
Leading automakers such as BMW, Honda, and Mercedes-Benz are harnessing this technology to enhance vehicle acoustics and expedite EV battery advancements. The AI systems delve into extensive datasets, leading to precise tweaks in engine settings and other components. This method is notably more effective than the conventional trial-and-error approach.
Generative design facilitates the swift exploration of numerous design variants simultaneously. It cultivates a culture of perpetual enhancement and innovation within automotive engineering and manufacturing. The technology bridges the industry’s skills gap by rendering sophisticated designs accessible to novices.
The data-driven methodology of generative design employs sophisticated algorithms to steer and inform design choices. This guarantees that proposed solutions are not just innovative but also empirically supported. Consequently, firms can expedite product validation, diminish design and development timelines, and incur substantial savings in material procurement, manufacturing, and logistics.
The Impact of 3D Printing on Automotive Prototyping
3D printing is transforming the realm of automotive prototyping. This method of additive manufacturing significantly accelerates the design cycle while concurrently reducing costs. Automotive manufacturers leverage rapid prototyping to swiftly produce complex components, a feat previously unimaginable.
AI-assisted 3D printing elevates this technology to unprecedented levels. These intelligent systems can anticipate and rectify issues instantaneously. This capability not only diminishes the number of printing iterations but also enables the creation of more complex designs. Consequently, it expedites the development process and slashes costs for the automotive industry.
The market for automotive 3D printing is poised for exponential growth. Projections suggest it will soar to $9.7 billion by 2030, with an annual growth rate of 15.94%. Leading companies such as Ford, Honda, and General Motors are already witnessing substantial benefits. Ford has successfully printed over 500,000 car parts at its Detroit facility. Honda, on the other hand, achieved a remarkable 50% weight reduction in a crankshaft through additive manufacturing.
Fused Deposition Modeling (FDM) is proving its efficacy in automotive manufacturing. It has been instrumental in creating an intake system for a racing engine, resulting in a 22% weight reduction and enhanced performance. As 3D printing technology continues to evolve, we anticipate seeing further innovative applications in automotive design and production.
Digital Twins and Smart Manufacturing in the Automotive Sector
Digital twins are revolutionizing the automotive industry. These tools create precise digital models of manufacturing processes. Automakers leverage them for optimizing production and predictive maintenance. The digital twin market is flourishing, projected to hit $48.2 billion by 2026.
Virtual factory modeling is pivotal for streamlining automotive operations. Digital twins can expedite critical processes by 30%. They enable manufacturers to simulate changes virtually, thus avoiding costly errors and enhancing efficiency.
Predictive maintenance is another significant advantage. Digital twins analyze real-time sensor data from production equipment. This foresight allows maintenance teams to address potential issues proactively. Consequently, it minimizes downtime and ensures consistent production.
Leading automakers are pouring significant resources into this technology. Companies such as Ford, GM, and BMW are integrating digital twins to elevate their manufacturing prowess. They collaborate with tech behemoths like Microsoft and Google to develop sophisticated AI and energy management solutions. These innovations are essential for optimizing production in the fiercely competitive market.
AI Copilots: Enhancing Productivity in Vehicle Assembly
AI copilots are transforming vehicle assembly lines, integrating with human operators to elevate manufacturing efficiency. Through the analysis of extensive data, they provide immediate suggestions for process enhancement. This synergy between human and artificial intelligence is redefining the automotive sector.
Retrocausal’s AI copilot stands out in this landscape. It meticulously observes the workflows of automotive production staff. It is reported to detect 80% of human errors, halve line-stopping occurrences, and expedite the onboarding process. These figures underscore the efficacy of AI in supporting workers.
The influence of AI copilots transcends mere error reduction. They are pivotal in enhancing processes in real-time. By scrutinizing assembly line data continuously, these AI tools can identify inefficiencies promptly. This facilitates swift adjustments, resulting in smoother operations and heightened productivity.
The automotive AI market’s expansion is driving widespread adoption of these technologies. Forecasts suggest the global automotive AI market will exceed $45.1 billion by 2024. This surge highlights the significance of AI copilots in vehicle assembly. They are not merely tools; they are essential collaborators in forging a more efficient, productive future for automotive manufacturing.
The Future of Automotive Production: Microfactories and Modular Manufacturing
The automotive sector is undergoing a significant transformation, gravitating towards flexible production methodologies. Microfactories are at the vanguard of this shift, heralding a new era in small-scale manufacturing. These diminutive, technologically advanced facilities leverage automated assembly cells to construct vehicles with unparalleled precision and minimal waste.
SAEKI Robotics is spearheading this technological evolution, designing intelligent systems tailored for these miniaturized production units. Such configurations enable manufacturers to effortlessly transition between different models, catering to the demand for bespoke vehicles or limited production runs. This adaptability is crucial in a market that values customization and efficiency.
This paradigm aligns with prevailing industry trends, as evidenced by Deloitte’s 2023 survey. A staggering 62% of industrial manufacturers are investing in robotics to expedite production, reduce costs, and address labor shortages. Furthermore, Grand View Research anticipates a substantial increase in the adoption of smart factory technologies, from 10% in 2020 to 50% by 2025, underscoring the sector’s commitment to innovation.
As the automotive landscape evolves, so too do the skill sets required within the industry. McKinsey’s analysis foresees a 30% decline in the demand for traditional skills over the next decade, while technology-centric skills are projected to surge by 50%. In response, automotive companies are enhancing compensation packages and investing in employee training to equip the workforce for the future of flexible, small-batch production.